Как снизить затраты на обслуживание железнодорожного транспорта благодаря оптимизационной модели
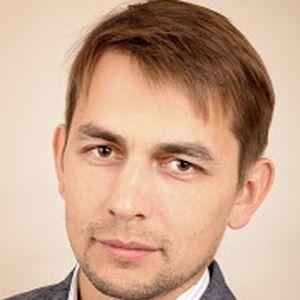
Чижов руководитель проектов имитационного моделирования офиса NFP компании "Первый Бит"
Оптимизационные модели позволяют компаниям производить реинжиниринг цепей поставок и рассчитывать как специфические показатели эффективности логистики, так и экономический эффект от внедрения тех или иных решений. Создание моделей и цифровых двойников дает ответ на вопрос сценарного анализа "что, если": что, если заменить поставщика ресурс; что, если спрос на продукцию в регионе вырастет на 10% и т.п. В современных реалиях оптимизационные модели позволяют бизнесу быстро находить наилучшую конфигурацию цепи поставок для эффективного импортозамещения и риск-менеджмента. Кирилл Чижов, руководитель проектов имитационного моделирования офиса NFP компании "Первый Бит", рассказывает о реализации проекта у крупнейшего российского железнодорожного перевозчика.
Предприятия с большим количеством складов в активе нередко сталкиваются с неэффективным использованием этих точек, а также распределением среди них запасов.
К нам обратился железнодорожный перевозчик, который осуществляет транспортировку горно-металлургических, строительных, химических и лесных грузов, а также промышленных товаров народного потребления. Среди подвижного состава – более 100 тысяч вагонов. Проблема состояла в неэффективном распределении вагонов по вагоноремонтным предприятиям и депо при выполнении планового обслуживания подвижного состава. Сеть компании насчитывала около 500 складов, которые снабжали запасными частями точки техобслуживания. При этом расположение запасов в сети было неоптимальным, зачастую их не было в наличии, и вагон простаивал сверх нормативного времени. Это приводило к упущенным продажам и финансовым потерям.
Перед командой проекта стояла задача оптимизировать источники и пути снабжения по критерию общей стоимости с учетом затрат и штрафов. Так как поставщиков и депо в сети компании много, классические подходы к расчету, например, в Excel, не работали из-за громоздких и сложных вычислений. Проектная команда приняла решение о разработке оптимизационной модели сети снабжения и производств компании в среде anyLogistix (программного обеспечения для имитационного моделирования).
В цепи поставок компании на момент старта проекта было:
- > 300 точек ремонта и техобслуживания;
- > 500 складов с запчастями и комплектующими.
Основные шаги при построении оптимизационной модели
Шаг 1. Понимание целей проекта, его ограничений и окружения
На данном этапе было важно провести ряд встреч с заказчиком, чтобы выявить реальные потребности компании, понять "боли" и проблемы. Часто случается так, что поставленные клиентом задачи не соответствуют его фактическим нуждам. В таком случае проектная команда на основе опыта предлагает свое видение решения.
Создание оптимизационных моделей – это всегда поиск баланса между уровнем детализации и точностью выдаваемых результатов. С одной стороны, максимальное приближение к деталям усложняют сбор данных для моделирования. Также снижение уровня абстракции приводит к перегруженности модели, а время расчёта сценария может стремиться к бесконечности. С другой стороны, создавая множество правил обобщения и снижая число параметров и ограничений в модели, можно упустить важнейшие показатели и построить несоответствующую реальность, другими словами, бесполезную модель.
В итоге решение было выбрано, возникло понимание необходимых допущений и ограничений, которые упрощают работу модели, но не сильно снижают ее точность. Пример такого допущения – ограничение числа складов, которые могут снабжать каждую конкретную точку ремонта, исходя из расстояния доставки. Такой подход позволил проектной команде снизить число моделируемых маршрутов доставки и повысить скорость расчета модели.
Шаг 2. Сбор и очистка данных
В ходе этого шага мы провели диагностику логистической цепи "как есть" с помощью оптимизационной модели. Были выявлены склады, недостаточно эффективно вовлеченные в процессы компании, а также участки с узкими местами, где простои из-за нехватки запчастей и комплектующих происходили наиболее часто.
Для совершенствования цепи поставок была дополнительно построена ничем не ограниченная модель GFA (Greenfield analysis – модель гравитационного анализа). Она показала, где именно должны были быть расположены склады компании с точки зрения мест наиболее интенсивного возникновения потребности в ремонте вагонов.
Также мы указали заказчику на полноту и достоверность некоторых существенных, получаемых с его стороны данных. Процесс их подготовки и очистки – наиболее важный при построении любых моделей, в том числе и цифровых двойников, так как используемые в инструменте anyLogistix (программного обеспечения для имитационного моделирования) методы линейного программирования не могут самостоятельно определять ошибки при заполнении данных. Следовательно, подавая в модель некорректные данные, невозможно добиться достоверности и точности выдаваемых моделью результатов.
Шаг 3. Создание прототипа модели
Прототип модели NO (Net Optimization – сетевая оптимизация) включал в себя не всех участников цепи поставок. Проектная команда совместно с заказчиком очертила границы прототипа: было выбрано 22 депо и 10 поставщиков в одном из регионов, для которых были смоделированы маршруты, потоки данных, уровни запасов и спрос на детали. Для обеспечения наибольшей эффективности модели в среде anyLogistix (программного обеспечения для имитационного моделирования) мы разработали сценарии с разной логикой и размерностью. Созданная модель и логика заложенных в нее расчетов была валидирована с помощью исторических данных: данные модели были проверены на сходимость с реальными показателями объектов цепи поставок.
Ниже на рисунках 1 и 2 представлены схемы цепей поставок прототипа: в виде графов и с расположением объектов на карте.
Рисунок 1. Цепь поставок прототипа в формате графов
Рисунок 1. Цепь поставок прототипа в формате графов
Рисунок 2. Цепь поставок прототипа на карте
Рисунок 2. Цепь поставок прототипа на карте
В итоге расчета прототипа встроенные отчеты инструмента anyLogistix (программного обеспечения для имитационного моделирования) выдавали информацию о том, какие перемещения были в цепи поставок в установленный период, а также вид транспорта, стоимость перевозок и процент загрузки авто. Фрагменты отчетов приведены на рисунках 3 и 4.
Рисунок 3. Отчет о потоках материалов в цепи поставок
Рисунок 3. Отчет о потоках материалов в цепи поставок
Рисунок 4. Отчет о транспортных затратах в цепи поставок
Рисунок 4. Отчет о транспортных затратах в цепи поставок
Шаг 4. Масштабирование и тестирование
Проектная команда масштабировала готовый прототип модели на все регионы, в которых работал заказчик. Также в ходе создания полной версии модели мы осуществили проверку логики потоков и балансировки модели, оценили ее точность и устойчивость при возникновении нестандартных ситуаций в цепях поставок. Исключения были скорректированы путем создания дополнительных правил в модели.
В том числе на этом этапе разработки решались проблемы нехватки вычислительных мощностей. Так как большие модели с наборами данных миллионов строк могут пересчитываться значительное время, важно проверить, не является ли заданный уровень детализации в модели излишним.
Результаты проекта
Созданная модель цепи поставок позволила железнодорожной компании пересмотреть использование 15% складских мощностей. При этом изменение частоты и номенклатуры снабжения точек ремонта привело к повышению оборачиваемости запасов на 5%, а простои вагонов в ожидании пополнения запасов нужными запчастями и комплектующими снизились на 8%. Всё это привело к уменьшению операционных логистических затрат на обслуживание подвижного состава компании на 4%.
В долгосрочной перспективе использование модели, а также ее модификаций для сценарного анализа позволят компании предотвращать инвестиции в недостаточно экономически эффективные проекты, а также проводить анализ устойчивости в цепях поставок при реализации рисков.
