Максимальная автоматизация - уже не фантастика
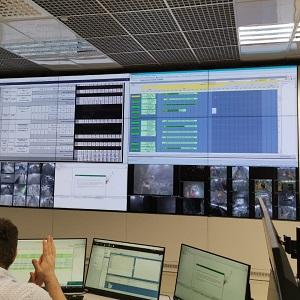
Радько
директор производственно-технического департамента "Норникеля"
"Норникель" запустил на руднике "Северный" Кольской ГМК в опытно-промышленную эксплуатацию АСУ ГР, - систему, позволяющую диспетчеру в режиме онлайн мониторить проведение горных работ и эффективно ими управлять. Запуск проекта стал возможен благодаря результатам многолетней работы по созданию подземной инфраструктуры, которая проводилась по программе "Технологический прорыв". О специфике внедрения подобных проектов в России рассказал директор производственно-технического департамента "Норникеля" Николай Радько.
Компания объявила о реализации проекта АСУ ГР. Не могли бы вы рассказать, что он из себя представляет и с какой целью реализуется?
- Цель у всех участников технологического процесса, у всех руководителей абсолютно одинаковая: повышение эффективности горных работ, оперативности получения информации и управляемости процессом.
Мы начали с рудников, создав инфраструктуру систем связи и позиционирования для обнаружения людей и техники под землей по программе "Технологический прорыв". Протянули под землей оптоволоконную сеть, установили Wi-Fi - систему беспроводной передачи данных, видеокамеры. Каждый горняк оснащен индивидуальной меткой, она считывается специальными устройствами, которые расположены в выработке. Метками оснащен и подземный транспорт. Транспондер позволяет передавать диспетчеру данные о местонахождении и передвижении под землей людей и техники.
Автоматизированная система управления горными работами - АСУ ГР, которая работает на базовой инфраструктуре проекта связи и позиционирования – это следующий этап. АСУ ГР помогает осуществлять непрерывный мониторинг горных работ, распределять объем работ, оборудования, подземной техники и как следствие обеспечить планомерную подачу сырья на обогатительную фабрику.
Горное оборудование в части цифровизации сегодня является достаточно "продвинутым". Практически все машины, используемые в подземных условиях, имеют широкий спектр контролируемых, по установленным на них датчикам, параметров. Кроме того, сама машина имеет множество собственных внутренних систем. И одна из основных целей и задач проекта АСУ ГР – это вывод параметров не только на блок управления самой машины, но и на более высокий уровень – диспетчеру, для того, чтобы руководство могло видеть и оперативно управлять всеми происходящими процессами.
В любой момент времени, находясь на поверхности, диспетчер может отследить состояние каждой единицы техники: работает – не работает, в каком режиме работает (в холостом или под нагрузкой), двигается – не двигается, бурит – не бурит. Есть ли в бензобаке топливо у машины и какое количество топлива. То есть, максимальный объем телеметрических данных, который можно снять сегодня с горного оборудования.
То есть, можно "снимать" данные не только о текущем состоянии подземной техники, но контролировать перевозку руды в режиме онлайн?
- Безусловно, да, это тоже телеметрия данных. На ковшах погрузо-доставочных машин (ПДМ), на кузовах самосвалов устанавливают датчики, которые передают информацию онлайн: сколько везет, куда везет и зачем везет.
Такая полная прозрачность становится возможной благодаря тому, что мы активно развиваем сети WI-FI связи внутри рудников, развиваем степень доступности всех уголков шахт. И эта работа выполняется большим количеством людей. В этом процессе задействованы огромные человеческие ресурсы, как самого "Норникеля", так и наших подрядчиков. Большинство решений, которые мы сегодня реализуем, носит в определенной степени новаторский и первопроходческий характер, поскольку готовых типовых решений, которые рынок сегодня мог бы нам предложить, нет.
Почему нет?
- Все фирмы-производители предлагают большое количество решений, в том числе и комплексные. Но каждый рудник по-своему настолько уникален, у каждого есть свои определенные задачи, которые заставляют производителя оборудования, технологий подстраиваться под конкретного пользователя. К сожалению, далеко не все производители оборудования, особенно импортного, готовы уходить от серийного производства к нуждам конкретного заказчика. Это, на мой взгляд, сегодня самая сложная задача. Чаще всего именно российские производители являются более гибкими, готовыми вносить изменения в конструктив, в параметры оборудования, так как они заинтересованы в рынке сбыта своей продукции.
Те, кто сегодня выпускает типовые серийные решения за границей, прекрасно понимают, что любое изменение своего оборудования под конкретного заказчика требует очень затратных предпроектных проработок, дизайна, инжиниринга. Вложения ради одного заказчика не окупаются, либо стоимость для него начинает в разы превышать стоимость аналогов, и, как следствие, становится не конкурентоспособной.
Например, есть совершенно замечательные сетевые приспособления западных производителей для WI-FI передачи - маленькие, компактные. Но все они не выпускаются во взрывопожаробезопасном исполнении. У нас шахты категорийные по газу, по пыли, у нас сульфидные руды. И это накладывает определенные требования на оборудование. Западные компании такого оборудования не производят.
Виталий Несис, гендиректор "Полиметалла", на "Майнексе" тоже говорил о необходимости новаторских разработок…
- "Полиметалл" двигается в этом направлении, но они в шахтах развивают сети 3G, сети LTЕ, строят свои сети коммуникаций передачи данных на основе мобильной сети. Мы же выбрали немного другой путь, делаем работу на базе станции WI- FI.
В чем вы видите преимущество WI- FI?
- WI- FI позволяет нам передавать по стандартным протоколам большой объем данных, с очень широкого спектра устройств, без использования проводов. Можно было бы растянуть провода по всей шахте, но поддерживать их постоянно в работоспособном состоянии было бы крайне затруднительно и затратно.
В качестве магистралей мы используем оптоволокно. По оптоволоконному кабелю мы можем передать огромное количество данных. Его использование позволяет значительно повысить пропускную способность и не только получать данные в виде цифр и голоса, но и видеопоток.
Возвращаясь к АСУ ГР. Прозрачность процесса является первым шагом к реализации решений по безлюдному управлению техникой. Сегодня мы все машины оснащаем датчиками, видеокамерами, но подземной техникой по-прежнему управляют находящиеся в ней операторы. Мы же, на данном этапе, начинаем учиться наблюдать и контролировать машины издалека. Следующим шагом будет процесс вывода оператора из процесса. Иными словами: сегодня оператор – своего рода элемент управления процессом, завтра у нас будет оператор как элемент контроля процесса, а послезавтра оператора уже вообще не будет.
Управленческие функции подземной техникой целиком перейдут в диспетчерский центр?
- Мы постепенно, постепенно стараемся максимально обеспечить автоматизированную автономную работу всего оборудования.
Основная цель – достижение производственной безопасности?
- Повышение безопасности, производительности и комфорта для сотрудников. Когда машинист ПДМ находится в кабинете, с кружкой кофе, управляет машиной всю свою смену непрерывно, это, согласитесь, намного эффективнее и качественнее, чем, когда он два часа добирается до своего рабочего места, получает наряд-задание, переодевается и тд. Таких дополнительных процедур, которые значительно сокращают эффективное, продуктивное время работы, достаточно много. При этом, у нас, безусловно, значительно увеличивается эффективность использования оборудования. Это уже конечная цель всего этого процесса.
Дальнейшая автоматизация не ограничивается только получением данных. Мы сегодня уже на многих рудниках пробуем формирование электронного наряда.
Что это вам дает?
- По старинке мастер приходит в нарядную при передаче смены начальнику участка, расписывается в журнале, получает задание. Опять же, это занимает время. Чтобы оптимизировать процесс, мы сегодня внедряем электронные паспорта, так называемые планшетные решения. Мастер, находясь с планшетом в шахте, двигаясь от забоя к забою, осматривая и констатируя состояние дел в каждой камере, сразу на планшете в режиме онлайн вносит в систему всю текущую информацию. Система сразу же "видит", что происходит в шахте, опять же, практически в режиме онлайн.
Если раньше наряды на следующую смену, на следующие сутки формировались по результатам смены, то сегодня эта информация уже начинает приходить не в конце смены, а во время нее. Это позволяет более эффективно составлять план на следующую смену, на следующие сутки, более эффективно использовать материальные ресурсы. Разумеется, эффективнее использовать технику, избегать ее простоев.
Своевременное получение информации о состоянии техники чрезвычайно важно. Иногда бывает так: машинист вышел на работу, выехал на линию в начале смены, машина была исправна. Через полтора часа в машине что-то застучало, зазвенело и, по идее, в такой ситуации ее нужно сдавать на осмотр. Но у машиниста своя задача, у него есть план, который нужно выполнить. Поэтому он будет до конца смены ездить, и только в самом конце сообщит мастеру. Мастер – механику и тот уже на следующей смене сможет приступить к осмотру.
Электронные паспорта позволяют к моменту окончания смены уже формировать задания механикам, энергетикам, другому вспомогательному специалисту. Люди оперативно могут направляться в те места, где работает данная единица техники, чтобы ее своевременно протестировать и принять необходимое решение: использовать ее дальше или требуется срочно ставить на ремонт.
Иными словами, вся эта система в первую очередь позволяет значительно ускорить весь процесс обмена данными. Из этого уже вытекает большое количество последствий, которые можно посчитать как в натуральном измерении, в тоннах добытой руды, так и в денежном измерении, в человеческих ресурсах. Эффект внедрения этих систем достаточно объемен и исчисляется огромными суммами.
Можно назвать эти суммы?
- Говорить об эффекте от внедрения отдельных систем было бы неправильно. Мы решаем комплексную задачу по переходу компании в новое целевое состояние, в котором будет выстроена эффективная система многовариантного планирования и автоматизированного оперативного контроля. Для чего и реализуется программа проектов "Технологический прорыв". На сегодня мы можем говорить об экономии на операционных и капитальных затратах в $44 млн и $12 млн соответственно.
В каком объеме АСУ ГР уже внедрена в компании?
- По разным рудникам внедрение находится на разных стадиях. Если говорить про Кольскую ГМК, там мы практически уже подошли к промышленной эксплуатации, соответствующие работы проводятся на руднике Северный. Если говорить про Норильск, то в рудниках Октябрьский, Скалистый и Комсомольский процесс близок к началу опытно-промышленной эксплуатации. Рудник Таймырский, рудник Маяк у нас пока еще на начальном этапе, рудник и шахта Заполярная; "Медвежий ручей" уже прошел 2 начальные вехи.
Вообще должен сказать, что АСУ ГР на подземных работах – это, наверное, самое сложное технологическое решение из всех существующих в мире.
Почему?
- Если вы заберетесь на башню "Федерация" в Москва-Сити, то вы сможете увидеть все, что происходит вокруг. Когда вы спуститесь в подвал башни, вы не увидите ничего, что происходит вокруг.
Аналогичные решения для карьеров, где идет открытый способ добычи, начали внедряться 15-20 лет назад и сегодня уже являются отлаженными, обкатанными. Еще на одном из наших активов – Быстринском ГОКе - система диспетчеризации и позиционирования была внедрена буквально за полтора года. Все было сделано оперативно, потому что на тот момент уже существовало типовое отлаженное решение.
Когда же мы сегодня говорим, что нам нужна доступность мобильной техники в шахте, то такого готового, отлаженного и обкатанного решения нет. К сожалению, подземные горные работы ограничены визуально, и сегодня нет таких технических устройств, которые бы пробивали километровый массив насквозь и позволяли доставлять сигнал в обе стороны.
Пока машина едет по прямой выработке, в которой есть датчики, все в порядке. Как только машина за угол повернула, машина тут же стала невидимой для датчиков. Наша задача не просто обвешать все выработки датчиками, что само по себе очень затратно, а создать такие решения, которые бы позволили видеть машину, даже когда она завернет за угол.
Николай Радько: "Когда техникой управляет человек, всегда есть пресловутый человеческий фактор: не заметил, устал, заснул"
Диспетчер должен видеть всю реальную картину в руднике и оперативно управлять процессом. Причем, визуализация на мониторе осуществляется не только через видео-поток, но и в цифрах. То есть, если едет самосвал, то диспетчер видит не только картинку с видеокамеры самосвала, но он видит также скорость движения этого самосвала, количество руды, перевозимой в этом самосвале. Опять же руду или породу он везет в этом самосвале, куда он везет, какой расход топлива у него в этот момент. Получает максимум информации, вплоть до того, какое давление в колесах в текущий момент. Это называется полная доступность всей информации.
Пока это звучит немного фантастически.
- На мой взгляд, фантастически звучало предположение, что когда-нибудь люди перестанут быть операторами, они просто будут сопровождать и обслуживать технику, потому что техника будет работать сама по себе. То, что это возможно, я поверил лет 10 назад, когда в Финляндии на заводе одной из фирм-производителей вживую увидел ПДМ, которая неслась без оператора в кабине. Было слегка не по себе, находясь в выработке, видеть, как мимо проносится многотонная машина, в кабине которой пусто, никого нет. Тем не менее, я могу совершенно точно сказать, что работа ПДМ без оператора намного безопаснее, чем с оператором.
Система работает и живет по заданным параметрам. Если задано двигаться со скоростью 10 км в час, то она будет ехать со скоростью именно 10 км в час, а не 25, не 50, как это делает иногда человек для того, чтобы ускориться. Система оборудована всевозможными датчиками, позволяющими своевременно останавливаться, есть понятие системы сближения и остановки. Любой человек под землей оснащен специальной меткой и при сближении человека с техникой, техника сначала начинает сигнализировать. При наступлении критических расстояний она сама останавливается и блокируется, чтобы избежать возможный наезд на человека.
Когда техникой управляет человек, всегда есть пресловутый человеческий фактор: не заметил, не увидел, было темно, не слышно, устал, заснул. Автоматика не устанет, не заснет. Безусловно, у нее тоже есть свои особенности, есть свои сбои, свои недостатки, но все эти недостатки "лечатся" путем совершенствования периферийного оборудования - большим количеством датчиков, большим количеством видеокамер, более современными анализаторами –всем, что технически исполнимо уже сегодня. И наша задача сегодня действительно оборудовать технику такими комплектами оборудования, которые максимально надежно работают и обеспечивают максимально точную достоверную информацию. Вот и все, простая задача. И это уже не фантастика.
Еще одним кирпичиком в нашей системе автоматизации управления горными работами является система суточного, сменного планирования. Система получает информацию от горного мастера о состоянии выработок - того самого планшетного решения; данные из АСУ ГР о готовности и наличии техники в рабочем состоянии, информацию о положении людей в забоях. И дальше строит планирование на определенные промежутки времени.
Она тоже пока еще имеет большое количество шероховатостей, сложностей, как технических, так и программных, и мы сейчас находимся в стадии отладки всех этих погрешностей. Пройдет некоторое время и к концу следующего года точно мы сможем уже с гордостью заявлять, что у нас в большинстве рудников внедрены системы, которые помогают эффективно управлять горными работами.
